In today's world of unique packages it's important for customers to take the time to research the equipment, the internet development very well, the quality machine and service surround you most important , BRENU is one of factory that give technical support for ever.

Before Order The Machine You Know
Are the machines upgradeable and adjustable?
Will they grow with your company?
Which features are standard and what comes as options?
Are the machines easy to maintain and clean?
Are they energy efficient?
Do the machines come with proper documentation and manual?
Are standard, custom, and wear parts readily available for the machine?
With the online service and all video ?
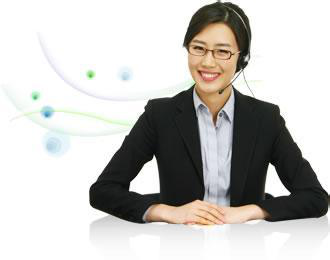

Why Choose Brenu?
Fast lead times and hands on demonstrations.
BRENU's practiced manufacturing processes, allow for some of the fastest lead times in the industry even on fully automatic and rotary systems.
A. Expert service, setup, and training on line or video
Maintenance, training, and installation are all services that BRENU offers customers. Proper installation and setup are key in getting new equipment working as quickly and efficiently as possible. BRENU understands this, and is why all BRENU machines leave the factory calibrated for each customer's individual needs. BRENU 's technicians also train our customers on how to maximize performance and reduce machine downtime.at the same time ,we supply the on line service by what’s app , we chat or others way .
B. Designing machines that grow along with the customer.
One of the key features of BRENU packaging lines are that they are designed to accommodate a range of different projects. BRENU knows that production needs change as time goes on and our lines are designed to grow with those needs. Each machine is engineered to handle a number of jobs and switch between those different jobs with little to no downtime. This makes BRENU machines a far better investment when compared to the limited capabilities of our competitor's models.
C. In stock and fast delivery of parts.
BRENU 10,000 sqr ft warehouse holds 27,000 different parts. All main components are marked for easy identification for both the customer and the parts technician providing fast identification and delivery.
D. Knowing and remembering our customers.
Record keeping : BRENU use modern CRM software to keep detailed account of everything including photographs, production log, bottle, cap, label, samples, right down to the machines birth day. We also installed rolling library racking to keep track of the thousands of machines their drawings, and customers
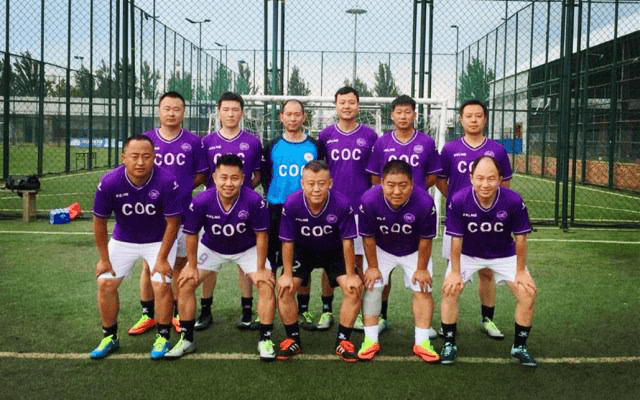